PEV Series Jaw Crusher
PEV Series Jaw Crushers: Efficient and Dependable
PEV series jaw crushers are widely applied in the fields of mining, metallurgy, construction, railways, water conservancy, and chemical industries. It is suitable for secondary or primary crushing.
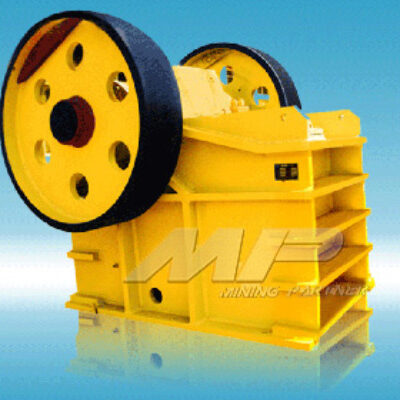
PEV Series Jaw Crusher Basic Concepts
There are now two ranges of models in the PEV series range. The first is the well-known traditional jaw crusher range that is designed for stationary as well as mobile applications (PEV80, PEV100, PEV 3054, PEV110, PEV125, PEV140, PEV145, PEV160, PEV200). The second range is designed specifically to meet the needs of small- to medium-sized mobile crushing (PEV96, PEV106, PEV116). All PEV series crushers are designed to crush very hard rock.
Whatever your crushing needs are, from hard and abrasive rock to various recycling materials, you’ll find the optimum solutions with the AF PEV series jaw crushers. Take a closer look at this jaw crusher.
PEV Series Jaw Crusher Terminology
The PEV series jaw crusher is a compression-type crusher. Feed materials are crushed between fixed and movable jaw dies. Large particles are crushed in a single layer, referred to as single-layer crushing. Smaller particles are crushed rock-on-rock, referred to as multilayer crushing.
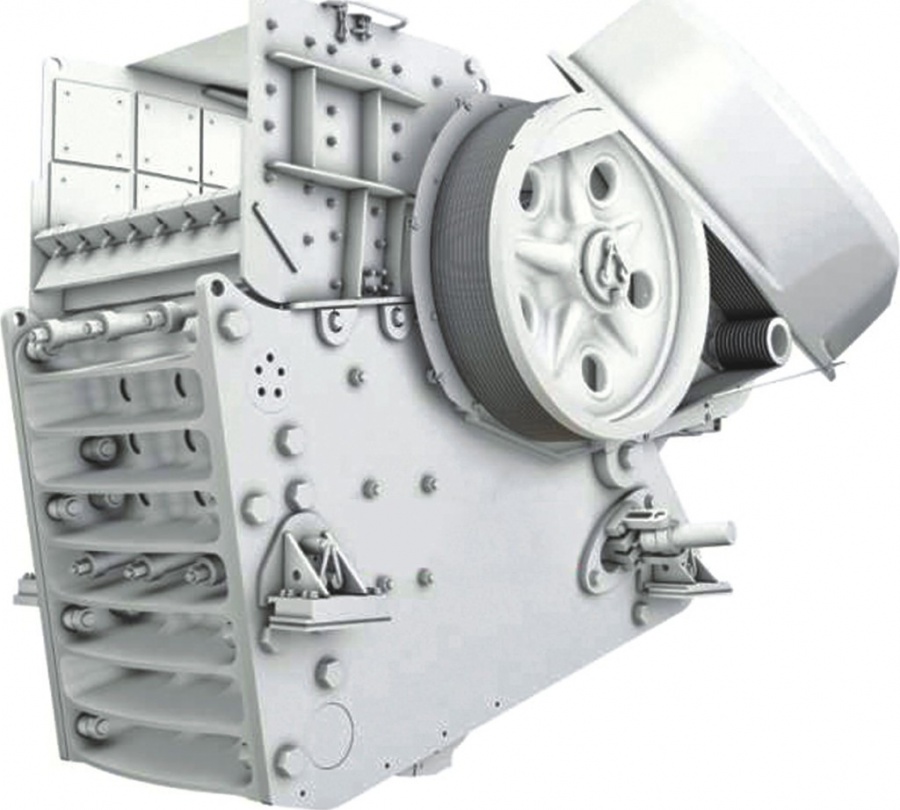
Feed Opening
Feed opening (depth of the cavity) defines the maximum feed size of the crusher. In the PEV jaw crusher, the feed opening is measured from the top of the tooth of the fixed jaw to the bottom of the tooth of the movable jaw in a straight line perpendicular to the centerline of the crushing cavity.
The maximum feed size is approximately 80% of the feed opening.
Open Side Setting (OSS)
The open side setting is measured when the crusher is at rest. The setting is measured either top-to-top or bottom-to-top, depending on the tooth profile of the jaw dies.
Closed Side Setting (CSS)
The closed side setting can be calculated by deducting the stroke from the OSS. CSS is the most important crusher parameter since it defines the maximum product size and has a significant bearing on capacity, product gradation, power draw, and wear. Check the instruction manual for the permitted minimum CSS.
Dimensions to be Deducted From the OSS for PEV Jaw Crushers
Nip Angle
The nip angle is the angle between the fixed and movable jaw dies. Too large of a nip angle reduces the capacity and increases the wear as the feed material grinds and gouges the jaw dies in an upwards direction during the compressive stroke of the pitman.
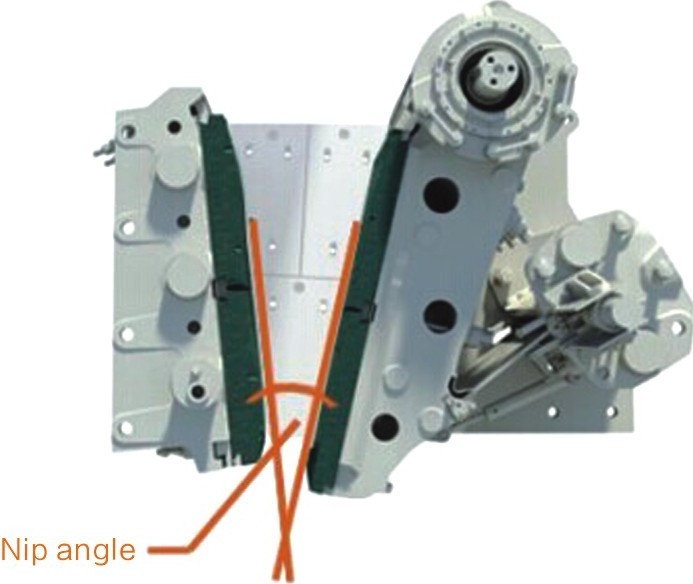
PEV Series Jaw Crusher: High Quality and Reliability
All AF PEV series jaw crushers are based on a revolutionary modular, non-welded frame construction. This design offers owners the highest possible fatigue strength, excellent reliability, and numerous mounting possibilities. This, combined with high-quality cast steel components and premium spherical roller bearings, means exceptionally high crusher availability, cost-efficient crushing, and low cost per ton.
World-Class Craftsmanship and Materials
AF PEV series jaw crushers are premium class crushers due to their design as well as to the materials that are used to produce them. Attention has been paid to even the smallest details to ensure the highest possible functionality and reliability, without any compromises. Those who have owned and operated PEV series jaw crushers know that not all jaw crushers are the same!
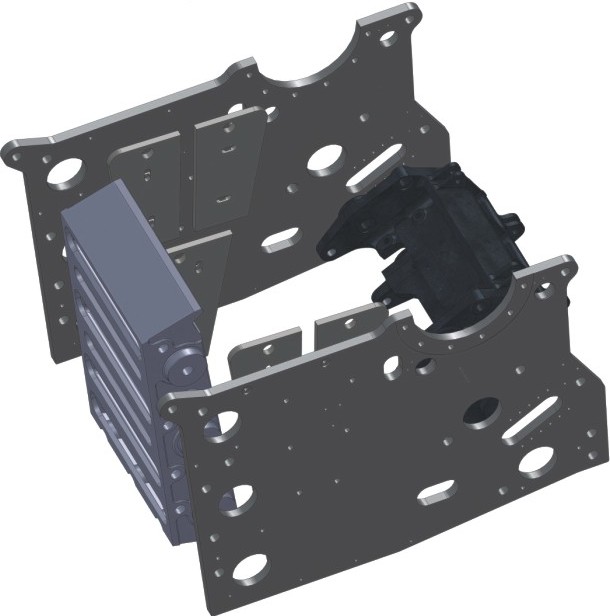
Modular, Non-Welded Construction
AF PEV series jaw crushers use a uniquely modular, non-welded frame construction. It is a state-of-the-art design with two hot-rolled steel side plates joined to high-quality cast steel frames through robust, precision-machined bosses secured with bolts. The absence of stress inducers such as weld seams ensures excellent durability against shock loads.
Durable Pitman Assembly
The pitman is made of high-quality cast steel and is propelled by two massive cast steel or iron flywheels. A very large eccentric shaft forging and four large spherical roller bearings that are all of the same sizes ensure the greatest reliability even under the most severe crushing conditions. The grease-lubricated bearings are kept free from contamination by means of well-proven labyrinth seals.
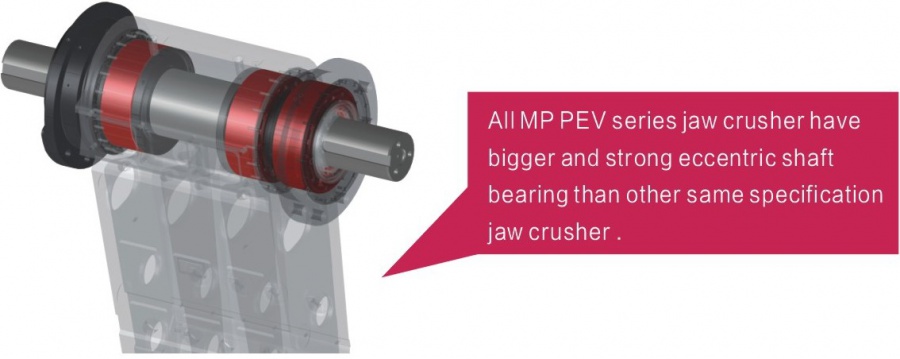
Single-Piece Cast Steel Frame Bearing Housings
The single-piece cast steel frame bearing housings ensure a perfect fit to the crusher frame. They also prevent unnecessary loads to the frame bearings that are common with two-piece frame bearing housings.
Repairable Crusher Construction
PEV series crushers constantly fulfill the durability expectations of their owners around the clock, but they will eventually need some care. Due to the use of cast steel components, the crusher can be economically reconditioned or rebuilt after many years of operation. Such repairs are uneconomical or impossible to carry out with crushers of alternative designs.
Durable Pitman Assembly
The pitman is made of high-quality cast steel and is propelled by two massive cast steel or iron flywheels. A very large eccentric shaft forging and four large spherical roller bearings that are all of the same sizes ensure the greatest reliability even under the most severe crushing conditions. The grease-lubricated bearings are kept free from contamination by means of well-proven labyrinth seals.
Aggressive Kinematics and High Power
In addition to the right cavity dimensions, the right kinematics must be applied. That is why PEV series jaw crushers have a large eccentric throw coupled with a steep toggle plate angle that magnifies the effective stroke at the crusher discharge. The large stroke, combined with the right speed, flywheel inertia, and high-available crusher power, results in truly high crusher performance.
Operation in small settings as well as the method of setting measurement results in finer products in comparison to other crushers.
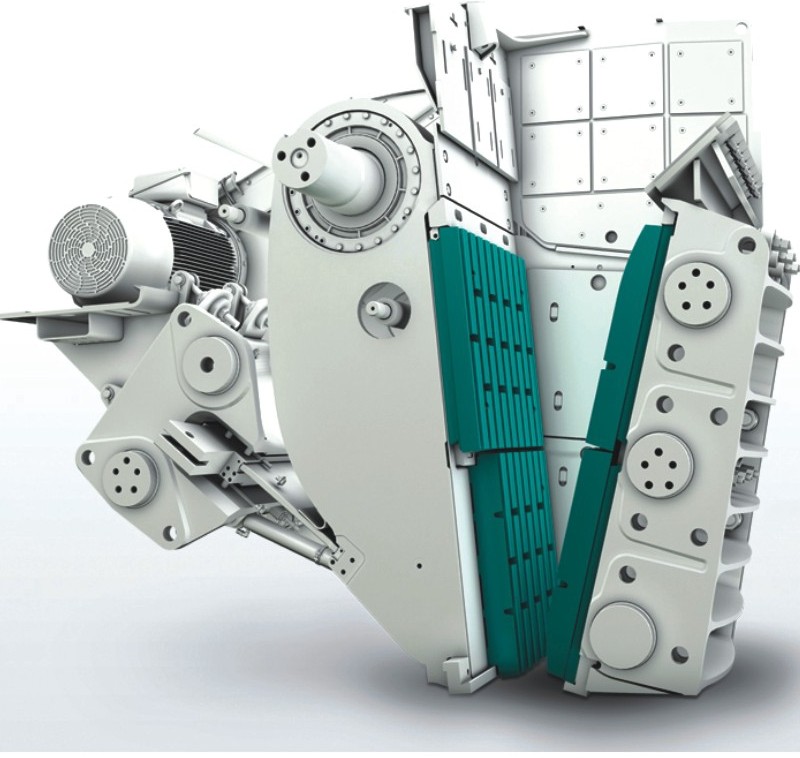
The Right Cavity Design
PEV series jaw crushers are literally designed from the inside out because the cavity is the heart and only purpose of the jaw crusher. That is why over the years, great attention has been paid to the feed opening dimensions as well as to the cavity height. The right feed opening width-to-depth ratio ensures minimum blockage and eliminates unnecessary height from the crusher.
One- or Two-Piece Jaw
Large PEV jaws (PEV110 and bigger) were originally designed to use a two-piece jaw die design, while the smaller jaw crushers used a one-piece jaw die design. A one-piece jaw design is now also designed for large crushers (PEV110, PEV120, PEV125, PEV140, and PEV160).
Benefits of One-Piece Jaw Die Design

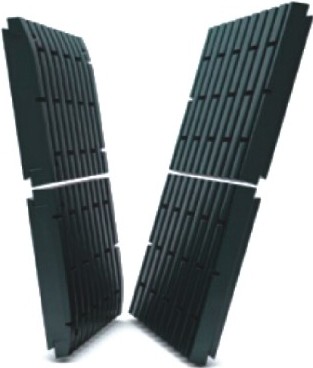
Benefits of Two-Piece Jaw Die Design
Many types of jaws have been developed over the years in order to optimize the performance of AF PEV series crushers in a very wide range of applications, including conventional quarries, mines, gravel pits, and recycling of demolition material and asphalt. The tooth profiles as well as the thickness of the jaws are optimized and combined with the right manganese steel alloys to maximize throughput and minimize operating costs. AF Minerals Equipment also so actively develops custom jaws for special applications. Special cheek plates are also available.
Standard
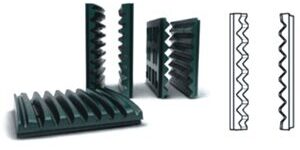
Super Teeth
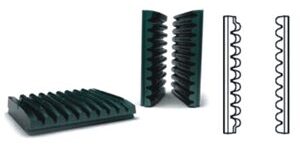
Super Grip
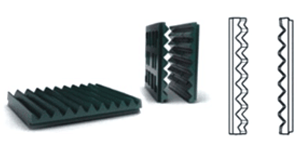
Quarry Thick + Super Grip
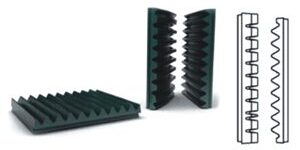
Quarry
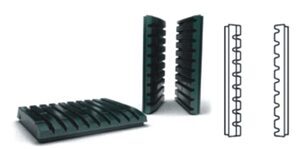
Quarry Thick
PEV Series Jaw Crusher: Low Installation and Operating Costs
In addition to bringing you high performance, PEV series crushers are also designed to bring your total crushing costs down. Each unique feature of the PEV series brings specific benefits that have a direct impact on the bottom line, which means that you will be more profitable. Those who have owned and operated PEV series jaw crushers know that not all jaw crushers are the same.
All PEV series crushers are equipped with a proven, rugged, and fast wedge setting adjustment system. The wedge setting adjustment is simpler, much safer, and faster than the outdated shim adjustment systems.
The crusher’s setting can be manually adjusted with tools that are supplied with the crusher in a matter of minutes, without having to handle dirty and bulky shims. Alternatively, the crusher’s setting can be changed in seconds, from a remote location, even while the crusher is idling! The system is also especially effective at clearing the crusher’s cavity should it stall under load due to interruptions in the supply of electric power.
Rubber dampers and stoppers effectively decrease crushing loads to the foundation by absorbing peak shock loads and allowing the crusher to move vertically and longitudinally. This unique and innovative system eliminates the need for anchor bolts and is a much more desirable solution as all anchor bolts eventually damage jaw crusher foundations.
All PEV series jaw crushers incorporate larger and sturdier eccentric shaft bearings than other crushers of comparable size. Their higher load-bearing capacity and effective labyrinth seals result in considerably longer bearing lifetimes.
The integral motor base reduces space requirements and maintenance costs. An integral motor base is mounted on the frame of the crusher, thereby reducing the need for space and excessively long v-belts.
The v-belt lifetime is prolonged because there is no differential movement between the crusher and the integral motor base, and the base pivots on the crusher in order to adjust the v-belt tension. It also accommodates both IEC and NEMA electric motors.
The use of the integral motor base allows for the use of standard flywheel guards, thereby eliminating the need for local engineering and fitting.
Flywheel guards are bolted onto the crusher’s side plates and effectively protect operators from the potentially dangerous moving parts. Viewing windows and access doors allow service crews to inspect and service the crusher. Their use also gives greater access to the crusher as the guards are not laying on the service platform.
The feed chute effectively protects the crusher and can be removed from the crusher for maintenance purposes. The feed chute is designed to effectively guide the feed into the crusher’s cavity. Jaw and cheek plate removal and installation are carried out without having to move or remove the feed chute. The feed chute is bolted to the crusher and can be removed for other maintenance purposes.
There are several additional features that will assist you in reaching lower operating and installation costs. Amongst these features are an automatic grease lubrication system, different mounting brackets to accommodate different feeding heights, temperature and speed sensors, protection plates, and intermediate plates in order to maximize the utilization of the Manganese jaws.
There are even special deflection plates available in order to protect the crusher discharge conveyor belt from sharp steel bars that are often present in recycling applications.
An intermediate plate can be used when feed capacity is low (empty cavity), feed size is small, or feed is slippery. It increases the length of the crushing area in case of an empty cavity or small feed size—better wear profile and longer lifetime. It also improves the nip angle, providing a better grip of the material in case the feed material is slippery.
Its restrictions include a decreased feed opening and maximum setting. These are reduced by the thickness of the intermediate plate.
Note: Crushing forces can be higher when using an intermediate plate.
Protection plates protect surfaces between the jaw dies on the pitman and front-end casting, especially when the material hardness and toughness are a concern or when crushing at the minimum setting. Protection plates are suitable for all applications and are delivered as standard equipment on large PEV jaw crushers, except for the PEV125. Protection plates can also be purchased for other size crushers as an option.
AF PEV series jaw crushers are the right choice for stationary surface installations at quarries, mines, gravel pits, and even recycling plants. Their ease of installation, serviceability, and productivity make them especially suitable for existing installations or new green-field primary crushing plants.
Due to their overall space requirements, PEV series crushers are an ideal choice for the replacement of existing double and single toggle jaw crushers. Foundation loads, when compared to those of older crusher versions, are less and therefore modifications to the existing foundation are rarely required.
An increase in plant capacity, the ability to process a coarser feed, and the ability to produce a finer product are common benefits when replacing double toggle as well as single toggle jaw crushers of comparable size.
AF Minerals Equipment designs and supplies complete aggregate crushing and screening systems. We are globally local and manage plant design, equipment selection, sourcing, manufacturing, installation, and commissioning. New primary crushing plants are tailored to each customer’s needs.
Various types of feed arrangements, automation, serviceability, and overall cost-effectiveness are the trademarks of our success.
Dimensions and Weights
- Crusher Without Options
- Crusher, Hydraulic Setting Adjustment, Flywheel Guards, Integral Motor Support, Feed Chute, Automatic Grease Lubrication System, and Typical Electric Motor
Note: Smaller closed side settings can be often used depending on the application and production requirements. For a performance estimation for your specific application, please contact AF Minerals Equipment.
The above figures represent the crusher capacities, which are based on a feed material with an average specific gravity of 2.7 tlm3, a maximum feed size that will enter the crusher without bridging and material finer than the crushers closed side setting removed. The capacities may vary depending on the feeding method and on feed characteristics such as gradation, bulk density, moisture, clay content, and crushability.
Measurement of the crusher’s closed side setting varies depending on the jaw profile that is being used and has an impact on the crusher’s capacity and product gradation. The following factors will enhance crusher capacity and performance:
- Proper Selection of the Jaw
- Proper Feed Gradation
- Controlled Feed Rate
- Sufficient Feeder Capacity and Width
- Adequate Crusher Discharge Area
- Discharge Conveyor Sized to Convey Maximum Crusher Capacity
Indicative Product Gradation
How to Operate a PEV Jaw Crusher
In order to get optimum capacity and maximum lifetime of wear parts, consider the following points:
Check the Feed Size
Oversized feed material decreases the capacity and can cause unnecessary stresses to the crusher components. Small feed size increases wear at the bottom of the cavity and may cause poor utilization of wear parts.
Check the Feed Arrangement
In order to reach optimum capacity and maximize the life of the wear parts, the crusher cavity should be full, and the feed must be distributed evenly across the crushing chamber.
Apply Proper Scalping
Fines (material smaller than CSS) should be removed from the feed material. This is done by the grizzly bar section of the feeder. Fines in the jaw crusher increase the percentage of contact area against the jaw dies. This increases scratching and grinding and reduces lifetime.
The Right Choice for Underground Installations
PEV series jaw crushers are indisputably the most popular crushers in underground mines and quarries all around the globe. Their productivity, reliability, ease of transport, and the possibility to automate make them an ideal choice for operations that run 24 hours a day.
Underground Assembly
The transportation of PEV series crushers to underground installations is greatly simplified as each major component can be handled individually and the final crusher assembly is done underground. This has a direct impact on mine planning that often results in considerable time and cost savings.
The final assembly underground requires typical lifting facilities and a surprisingly short amount of time.
Easy to Automate
Due to their hydraulic setting adjustment, PEV series jaw crushers can be fully integrated into plant automation systems. The setting of the crusher can be changed from an electrical cabinet next to the crusher or the operator’s room, all at the touch of a button even while the crusher is idling. The lubrication of the crusher’s bearings can also be automated.
Bearing temperatures, crusher speed, and cavity levels can all be measured and fully integrated into plant automation systems.